视频专区
Current Location:HOME
- Author:
- Source: 北京SMT专业委员会
- Date: 2016-11-08
- Views: 4336Times
作者:余翠丽 刘汝国 蔡三强
本文所指小批量试制多为数量小于10块的PCBA试产,客户的期望多是尽快验证PCBA功能的正确性。产品物料规格一般在250种以下,数量多在5K以下。物料中IC pitch多是0.5mm或以上的BGA、CSP、QFN、SOP、LGA、QFP。pitch为0.4mm的仅为QFN、QFP及表贴的连接器。经常有个位数以内的压接件及数十个插件物料。PCB常为多层板,表面处理一般是HASL或ENIG。
本文所述低成本只是对于制程方式的改进, 力求使占用生产线的时间得到有效减少。当今工时费用北京大约在45元/人.H左右,SMT生产线一般配3至4人,整条线工时费用一般在500-1000元/L.H。较复杂的产品可压缩50%以上的占线时间,一般产品的占线时间多在单面2H左右。表一中给出某司几款产品的信息及占线时间(某司加工环境:1、库房提供产品的齐套物料;2、产品在生产过程中,从BOM整理核对到物料整理,从机器编程到上料贴装,再到焊接直插件,基本上是一个人负责处理,还有相当大的改善空间)。 表一
以下按导入时序,自文件处理,含贴片程序制作及虚拟首板确认,简易SOP(手贴、手吹……)做成,物料管理,网板工装导入,现场管理,质量成本的管理。介绍一下我们的实践与体会。鉴于笔者所供职过的公司多属小微EMS企业, 片面性和局限性是必然的。
由于人的配合在短的磨合期内将导致较高的效率损失,人员的安排应尽可能的少。SMT制造现场操作员两人即可,贴片工序一人操作贴片机,另一人同时并行手贴,其余工序两人合作完成。SMT现场无专职QC人员。现场人员要敢于做主,一旦开工,不再向项目责任人(多属工艺人员)以外的任何人请示。不能判定的一律跳件,除BGA、QFN外。手工对应其它所有的封装不符的物料,于线下并没有多大难度。同时记录所有的问题,收线后逐一与客户核实解决。
以下与常规操作相同的手法原则上不再介绍。
一、文件处理
大牌EMS对NPI有多达一百五十余项的check list,而我们一般仅能得到BOM及部分Gerber (B/T面焊盘层,白油标识层)与CAD数据,处理时手段有限。
1、BOM的审查与整理:从实践来看,QC应使用客户的原始BOM,而工程、工艺、制造则使用整理后的BOM。本文记做(BOM),它应具备如下信息:序列号,品名(含规格与封装),用量(含T/B面各多少),位号(T/B面差异性标识,多数人用不同的颜色手工标识。若是用不同的字体区分,当然是用计算机以比对的方式自动生成,可大幅减少人工干预出错的可能性,并可使查错变得更容易。若定义每一行的位号个数。则可进一步减少后续的确认工作量。位号描述要杜绝连续位号采用的各种缩写方式,当有不贴件用NC注示时不要删去,但可用{ }标识,以便和原始BOM易于比对)。备注(此栏要有工序的区分栏,把机贴、手贴、手吹、压接/插件焊接与组装四大项用缩写标明。代用物料及变更在此标明出处,如在此备注行标注<1>,而在(BOM)最后写明<1>是2014.3.8陈工邮件。所有应消除项要留原文字用{ }标识,所有后追加文字用[ ]表示是追加,所有不确定的问题项用明黄色标识后尽快向客户确认。并力促客户仅在BOM上做修正,明示不同点,不要再次发不同的BOM。则可有效降低处理文件的工作量。
2、贴片机程序制作及手贴手吹物料的确定:应用常规软件判定一下位号的单一性与位号和数量的相等性再产生程序。程序生成不考虑线平衡,优先单机生产。不优化程序,配列表显示料站与(BOM)序列号的关系。物料封装为0402及以下时优先吸嘴低速运行及拾取。
机贴物料的确定原则是使用数量大的带状料,T/B两面均用者优先(数量小时或送料器不够时)。并且在T面与B面生产时该料站固定。使用量小的(如五个以下)齐头料,散料,管状料及细间距以外的BGA,QFN一律优先手贴。当手贴的工作量大于两小时(手贴效率按400P/H),把多余的工作量做为手吹处理。此工序物料优选CHIP电阻(0603及以上有标识),塑封二极管,SOT23。磁芯线绕电感电极采用搪锡工艺且电极平整度差时,优先归于手吹工序。简易的手贴、手吹等作业指导书不过是写出其工序所用物料在(BOM)上的序列号,使用时配合找位置软件即可。
3、找位置软件准备:该软件是某实验室自行开发,较类似软件优点是除按位号寻找位置外,还可采用封装形式、 规格、方向(吸嘴转动角度)为选项。可选择在板边(如图一边框处)与定位点(图二焊盘间)同时显示, 并可仅显示板边, 或仅显示定位点等三种显示方式。以Gerber为平台精准指示相关位置。并可使众多同类别选项同时显示,较一些品牌软件也极具特色。当显示屏幕足够大时,用于虚拟首板确认,其优势将更加明显。当贴片程序(来自(BOM))被导入此软件后,配合与BOM核对。在用于虚拟的机贴物料的首板确认时。可挤兑出自BOM转换(BOM)时可能的错误。而导入项为(BOM)与CAD时,则可根据工序分类按规格生成手贴、手吹、插件等简易作业指导书。
图一:选择参数值部分电容10N 0402,找到76个匹配项,板边和定位点同时显示。
图二:对图一文件进行局部放大。
4、虚拟首板确认:把贴片程序中的位号与坐标导入到找位置软件,注意此时的原点与Gerber并不一致,应做offset修正。再按(BOM)的序列号从小到大,逐一选择机贴物料规格为显示项。则所有相应的位号可显示在GERBER示图四周(板边),如图一。以这些依次排列的位号与BOM中相应的位号对照并用铅笔标注,可以确认程序中位号数量与位置的正确性。此时标识点(定位点)剪头方向对应于物料的极性如图二,可以做为极性正误的判据。当选用标识点显示在贴片焊盘位置正中时,如图四。则可判定坐标位置的正确性。因许多物料的CAD数据并不以器件的几何中心为基准,在此可以根据标识点与焊盘的非对称性提前识别,免得上机后才发现座标有误。另一识别是按封装如0805为选项。如图三显示,看所有0805焊盘大小是否一致,以便事先发现物料与PCB 上相应焊盘的不一致性。
图三:选择封装形状0805封装找到57个匹配位置,只显示定位点边提示。
图四:对图三文件进行局部放大。
5、 丝印机、贴片机支撑图准备:印刷机B面的支撑图,当用平面支撑时可省略。其余的要用透明薄膜以1:1的方式把GERBER图B面与T面的位号及焊盘层打出。支撑的选点要把二者重叠后确定。用于B面的支撑点要尽量避开T面的BGA、QFN等各种微小焊盘,用于T面的支撑则要尽可能撑实BGA、QFN、连接器等细间距物料下方。同时要防止碰伤B面物料。固定间距的支撑销较磁性支撑销有更多的限制(若能采用可变间距支撑销则可有较好的结果)。应配合定间距网格选点,同时注意STOPER的影响。选点完成后用红色油性笔在透明膜上做记号,并标出进板方向。编号说明产品名称,适用机器及适用面。从质量成本考虑,支撑不论对印刷机或贴片机,都是极其重要且最易被人忽略的品控关键点。
二、 物料管理
1、物料的接收: 要尽量简化,小批量时来料多为小段齐头料,托盘料一般也都不正规。某司早期接料经由市场,采购,库房以及IQC,才到生产班组。反复的清点与检查,使物料状态更加恶化。变形,可焊性变差,在貌似正规的制度下造成了许多可避免的麻烦。事实证明,物料直接由专职操作员接收是较好的选择。该人负责发料清单与(BOM)的对应及核实。重点是物料的规格及封装,对chip件的数量确认不应强求。称重是应首选的确认数量的手段。
2、物料的标注:在物料的最终包装上贴上纸胶带,写上(BOM)中该物料对应的序列号。再根据机贴程序,手贴工艺,手吹工艺、手焊工艺(含压接,铆接,组装)分别标注缩写。如:机,手,吹,焊。并要标出用于哪一面。在T面标T,在B面标B,T与B面均使用时标T/B。标完后按T面, B面及T/B面及工序分开放置。以利于工作时有序找料。且在(BOM)序列号处做有料标注,以便核对(BOM)上所有物料是否己齐全。注意在物料的标记时,要确认实际封装如0805与(BOM)所写封装的一致性。当发现预定机贴物料有变形及不适上机的状态及时转手贴。要鼓励此时对前期文件处理的修正。
3、物料关注重点: 首先要判断PCB是否有电测试痕迹,用30x放大镜看焊盘上的针痕。若无,(BOM)备注上应标出。并测裸板各电源端对地有无短路(以后各工序都增加对各路电源的短路判定)。PCB一般应无条件烘烤且整平,注意工艺边是否足够,有问题标在(BOM)上。小批量时不影响功能的缺陷,当有可能影响交期时应考虑放行。同时告知客户。确认所有极性元件是否在PCB上有相应的白油标识,若无则应在PCB上做永久性极性标识。有金手指,金键盘时要事先于办公区做贴保护,有试锡板时确认一下可焊性。对PCB上BGA类的非可视焊点焊盘,有疑似可焊性不良时,可用烙铁手工上锡后整平待用。PCB外形的目视检查重点是夹持边的毛碴。
其次是接插件、压接件、铆接件都要试插或者比对一下,如果物料不适,优先改造PCB以适应物料(在裸板状态,修改起来要简单得多)。
QFN电极如立面无涂复保护,且疑似可焊性不良时,应手工在电极立面搪锡。
4、网版与工装的导入:项目工程师要参与对物料的查看,以异型贴片件和未见过的封装为重点。一定要认识到,当你不能干预PCB的DFM时,网板开口的补救措施是最有效的品质保证手段。一般是把异形物料电极向上放在焊盘旁,目视其间的差异。按网板开口原则处理(参照贾忠中[SMT核心工艺解析与案例分析] 一书)。当有PITCH<0.5mm的物料时,OFFSET式网板开口在焊盘间有走线,但无阻焊层时应优先考虑。
当你在短时间内,对确认印刷参数无把握时。网板厚度宜薄,以得到稳定一致的焊膏量。开口宜稍大以对应小批试制时物料可焊性多数无保证这一事实。在网版面积许可的条件下,可在一块网版上有两个不同的开口设计方案,以增加现场的对应能力。最好能采用局部DEK膜工艺。对纳米涂料的预分装及热合再封装是低成本的要点。
工装因使用次数少应采用低价材料,但关键部位要采用高精度的加工方式以保证使用。其余辅助部分可用后粘合方式,以降低成本。
有面积较大的压平结构时要考虑实际效果,尽量不采用面对面的压平方式。用线对面的压平方式低成本,灵活性好,效果也好。
测温板应使用产品用PCB,关键器件只能采用替代品,在厚度及体积方面的相似性越大越好。能有类似的报废板由客户提供是最佳选择。热电偶选点参照“测温板制作方法”(参照2014论文集 三重 尹华春)。
炉温曲线的确定应事先完成。应偏向直通率考虑,峰值就高不就低。充分考虑物料特性,如焊球合金成分,BGA的尺寸,厚度,类型。铝电解,接插件要事先过炉看其温度耐受性能。对薄板,多层板的二次过炉优先考虑简易载具,保证PCBA的平整度。室温至峰值时间与焊膏特性差异要小,在含微小焊盘的生产时尤为重要。提倡上下温区差异化的设置方式。
三、现场管理
1.物料准备(上线两小时前应已完成)
1-1、所有托盘料的烘干,首选真空烤箱 125°C/2~4H。
1-2、无铅工艺PCB或多层PCB参照上条。
1-3、金手指,金键盘贴保护(于无焊料粉的办公室或会议室)。
1-4、PCB编号并标识,无测试痕迹时所有电源回路短路判别并记录。
1-5、QFN电极立面无涂覆,且可焊性疑似不良的器件手工在立面搪锡。
1-6、锡膏回温4H,再甩90s。
1-7、PCB贴无残留膜,最少四块。
1-8、网板清洗,有脱模不良可能时局部涂DEK膜(纳米涂料要分装,一分四后用热压机封口。每1/4包装可对应4~5块网板的局部开口)。
1-9、准备精密天平(精度10mg),所用焊膏的原厂供助焊膏。水金PCB或疑似物料可焊性不好时,应在陶瓷板上做试验。确认不良后加总重0.5~1%的助焊膏。
1-10、HASL板MARK的平整度确认,应小于15um。否则用烙铁与吸锡绳抹平后用黑橡皮打磨。
1-11、所有支撑,工装的清扫。
1-12、手贴件与手吹件分别连料带用双面胶粘在防静电板上,每种料都标明(BOM)的序列号及单板用量,并标出单板用量所对应长度。
1-13、无标识的CHIP料要用LCR表判别其阻抗正确性。
2.印刷工序
2-1、所有未贴膜的PCB用胶滚去异物。
2-2、利用支撑图快速建立支撑,B面时优先用平面型支撑。
2-3、真空清扫口两边用胶带封住,仅留和PCB等宽开口(国产机尤是)。
2-4、试印第一块贴膜PCB,检查位置偏差并纠正。最少陆续印四块贴膜PCB后,才可正式印刷。
2-5、正式印第一块生产用PCB,此时最小开口的脱模状态可能会劣于贴膜PCB。若在可接受的下限时,则每次清扫都要选择真空模式。慎用压缩空气吹或用湿巾以手工模式过度清扫,那样会使开口壁上助焊剂流失。而使转移率进一步下降。
2-6、在得到可接受的印刷结果后尽快全数印完。有缺陷时,按PCB编号记录缺陷位置,本着宁修勿冼的原则,尽量不要清洗印刷失败的PCB。能有富余的PCB备份为最好。否则用银针补焊膏,但应取自试印膜上相应焊盘的焊膏。焊接后在该位置用目视或者X-ray重点检查。
2-7、印刷机收尾由机贴操作者完成,其在下工序工作时间以及内容要少于手贴操作者。
3.贴片工序
3-1、手贴在第一块PCB印刷完毕后尽快开始,要与机贴并行工作。手贴建议同时贴几块板的同一种料,而不是一块贴完再贴一块。这样对出错率和效率都有好处。
3-2、手贴完一块板后,要在料带旁标识以证明所用数量是正确的。每一种物料在单板贴完后应在粘料板上写出相应PCB编号。在出现问题时可用较少的时间判定症结所在。
3-3、手贴工具以吸笔为好。当用防静电镊子时,歪件后尽可能拨正即可,不要重夹起来。镊子尖要勤清扫,贴放后应有点压动作。除QFN外,较大封装IC尤应施加较大的压力。
3-4、QFP,SOP引脚疑似可焊性不良时,引脚没入膏的深度较大时焊后结果会较好,但chip类则不应有焊膏被挤压的痕迹。
3-5、当有印刷错位时,贴片应以焊膏为基准以得到尽可能满意的结果。
3-6、当某局部间隙极小(如0.13mm以下)时或对位置要求很高(v-cut槽旁)。灵活运用offset模式贴偏一些,让chip在回流时自动找正位置可降低不良率。在LGA对空洞要求严格时也可斜方向贴偏0.05mm。
3-7、当贴片收尾有少料情况时,一律不找料。跳过后按PCB编号记录即可,以后以修理手段补上。
3-8、推定易产生吸着不良的物料,如0402及以下chip或者较重的物料。要放慢吸取及运行速度。在首板时,每贴100件chip要停机检查一下有无飞片现象。500件后无异常则可不再停机检验。可能时优先贴非chip物料。
3-9、生产最好安排在周保养后,至少要清洗吸嘴并更换过滤棉。
3-10、大件,高重心,易浮起件应是炉前检查重点。安排在炉前过桥处手贴。机贴已完成的PCB,手贴时优先贴BGA,QFN等焊点不能直视的物料。
3-11、首板机贴后没有停机确认的过程,立刻打第二块板。然后仅确认首板机贴件的方向是否正确。不能确认的做记录。
3-12、变形的器件要修正后再贴,并做记录以利最终的针对性检验。
4.回流工序
4-1、炉前检验所有有极性器件,压实易浮起器件。
4-2、B面原则上一律走网,给T面印刷打好基础。
4-3、进炉时PCB间距尽可能大于板长的3倍以上。
4-4、走网时避开通长的网带支撑条,至少使其不位于关键元件下方。首板过炉前可放2块热容量相似的PCB于其前方3倍板长处。
4-5、首板的焊接状态确认后方可接着过板,重点确认BGA的塌陷程度和大型物料的焊点状态(有无冷焊),微小焊点(0402或者以下)有无葡萄珠现象。微小物料有无因风速导致的缺陷。连续过板完成后,马上两人同时收线,尽快让他人转线进行下一产品的生产。
四 质量成本管理 (以下与占线时间无关)
1-1、炉后尽量使用叠式存储器放置刚出炉的PCBA,在托盘立放可能使PCBA产生翘曲,且板边的物料有与托盘凹槽碰撞的可能。
1-2、单边尺寸大于150mm的PCBA不可单手持着,一定平放在有防静电海绵的钢性托盘上,后工序均应按此处理。
1-3、BGA目检后用无残留胶带封住四边间隙,按手吹指导书完成剩下的贴片料焊接。原则上仅能使用热风枪。
1-4、目视检查重点是曾出现印刷缺陷的焊点和疑似可焊性不良的物料的焊点。所有不良处用红箭头标识指出。
1-5、不良点的修理完成后在红箭头上用笔标识。在QC确认合格后并填写直指原因的修理记录后, 撕去红箭头。
1-6、铆接时注意方向,手工压时可分两三次加力完成压铆,以减少可能的失手,机压时尽可能放慢速度。
1-7、压接每种规格物料的第一个时要尽可能慢,PCB与下模的对位与方向性要格外小心。从成本出发,小批量时手工为宜,最好不要一次压到位。每次加压后要检查有无跪腿现象。上模一定要用高精度的,事先要用实物验收,看精度是否合适。当有两个压接件紧密排列时要注意上压头的外型是否会干涉先前压好的件。压接件孔径要事先确认。HASL孔可用合适的钻头过一下,以消除喷锡使孔径变小的缺陷。
1-8、直插件尽可能成型为短插以消除以后的剪腿工序。
1-9、当透过率不好时应该避免两面焊,用热板以125°的温度预热并在引脚上用助焊笔凃助焊剂是比较好的选择。
1-10、多引脚物料先对角定点,确认无浮起后方可进行下一步的焊接。
1-11、晶体的金属外壳原则上不要焊接。
1-12、无铅的手工焊接要时刻想着铜蚀的风险,用SAC305锡丝的风险远大于锡铜焊锡丝。
1-13、有分板需求时一定要小心应力的作用,没有可靠对策时,切忌蛮干。
1-14、包装要用ESD材料,箱内空间要填实,充分考虑运输中可能出现的野蛮状况。
1-15、一般不采用在线AOI。
1-16、BGA, CSP, QFN尽量全数过x-ray,重点是查虚焊。
1-17、目检采用比对方式,如用1号板与其余板对照检查。标记出差异待核实。首先看空焊盘的一致性。重点是非机贴物料的方向以及标识的一致性。焊点目视重点是模块以及QFN。其次是细间距的QFP,SOP以及连接器(p<0.5mm)以及有整形记录的物料的焊点。
1-18、把DFM相关内容反馈给客户以便今后从源头解决问题。写试制报告, 所有不良项要认真解析, 并总结在时序上的浪费。
致谢:感谢曾经的团队成员陈克鑫、冯桂玲在多次的实践中提出的宝贵建议及在现场不懈的努力。
如需看完整的技术文章:请订阅印刷版《SMT工艺与设备》杂志/电话:0755-25856945
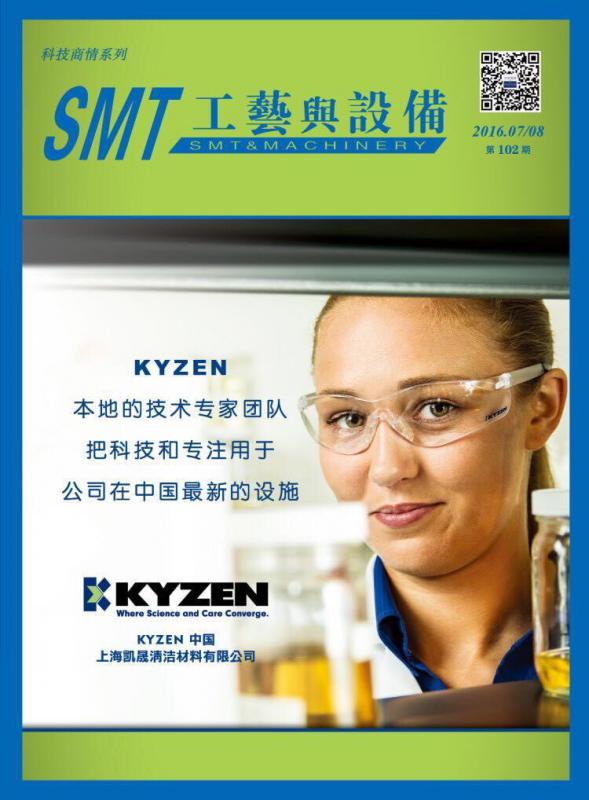
本文所指小批量试制多为数量小于10块的PCBA试产,客户的期望多是尽快验证PCBA功能的正确性。产品物料规格一般在250种以下,数量多在5K以下。物料中IC pitch多是0.5mm或以上的BGA、CSP、QFN、SOP、LGA、QFP。pitch为0.4mm的仅为QFN、QFP及表贴的连接器。经常有个位数以内的压接件及数十个插件物料。PCB常为多层板,表面处理一般是HASL或ENIG。
本文所述低成本只是对于制程方式的改进, 力求使占用生产线的时间得到有效减少。当今工时费用北京大约在45元/人.H左右,SMT生产线一般配3至4人,整条线工时费用一般在500-1000元/L.H。较复杂的产品可压缩50%以上的占线时间,一般产品的占线时间多在单面2H左右。表一中给出某司几款产品的信息及占线时间(某司加工环境:1、库房提供产品的齐套物料;2、产品在生产过程中,从BOM整理核对到物料整理,从机器编程到上料贴装,再到焊接直插件,基本上是一个人负责处理,还有相当大的改善空间)。 表一
以下按导入时序,自文件处理,含贴片程序制作及虚拟首板确认,简易SOP(手贴、手吹……)做成,物料管理,网板工装导入,现场管理,质量成本的管理。介绍一下我们的实践与体会。鉴于笔者所供职过的公司多属小微EMS企业, 片面性和局限性是必然的。
由于人的配合在短的磨合期内将导致较高的效率损失,人员的安排应尽可能的少。SMT制造现场操作员两人即可,贴片工序一人操作贴片机,另一人同时并行手贴,其余工序两人合作完成。SMT现场无专职QC人员。现场人员要敢于做主,一旦开工,不再向项目责任人(多属工艺人员)以外的任何人请示。不能判定的一律跳件,除BGA、QFN外。手工对应其它所有的封装不符的物料,于线下并没有多大难度。同时记录所有的问题,收线后逐一与客户核实解决。
以下与常规操作相同的手法原则上不再介绍。
一、文件处理
大牌EMS对NPI有多达一百五十余项的check list,而我们一般仅能得到BOM及部分Gerber (B/T面焊盘层,白油标识层)与CAD数据,处理时手段有限。
1、BOM的审查与整理:从实践来看,QC应使用客户的原始BOM,而工程、工艺、制造则使用整理后的BOM。本文记做(BOM),它应具备如下信息:序列号,品名(含规格与封装),用量(含T/B面各多少),位号(T/B面差异性标识,多数人用不同的颜色手工标识。若是用不同的字体区分,当然是用计算机以比对的方式自动生成,可大幅减少人工干预出错的可能性,并可使查错变得更容易。若定义每一行的位号个数。则可进一步减少后续的确认工作量。位号描述要杜绝连续位号采用的各种缩写方式,当有不贴件用NC注示时不要删去,但可用{ }标识,以便和原始BOM易于比对)。备注(此栏要有工序的区分栏,把机贴、手贴、手吹、压接/插件焊接与组装四大项用缩写标明。代用物料及变更在此标明出处,如在此备注行标注<1>,而在(BOM)最后写明<1>是2014.3.8陈工邮件。所有应消除项要留原文字用{ }标识,所有后追加文字用[ ]表示是追加,所有不确定的问题项用明黄色标识后尽快向客户确认。并力促客户仅在BOM上做修正,明示不同点,不要再次发不同的BOM。则可有效降低处理文件的工作量。
2、贴片机程序制作及手贴手吹物料的确定:应用常规软件判定一下位号的单一性与位号和数量的相等性再产生程序。程序生成不考虑线平衡,优先单机生产。不优化程序,配列表显示料站与(BOM)序列号的关系。物料封装为0402及以下时优先吸嘴低速运行及拾取。
机贴物料的确定原则是使用数量大的带状料,T/B两面均用者优先(数量小时或送料器不够时)。并且在T面与B面生产时该料站固定。使用量小的(如五个以下)齐头料,散料,管状料及细间距以外的BGA,QFN一律优先手贴。当手贴的工作量大于两小时(手贴效率按400P/H),把多余的工作量做为手吹处理。此工序物料优选CHIP电阻(0603及以上有标识),塑封二极管,SOT23。磁芯线绕电感电极采用搪锡工艺且电极平整度差时,优先归于手吹工序。简易的手贴、手吹等作业指导书不过是写出其工序所用物料在(BOM)上的序列号,使用时配合找位置软件即可。
3、找位置软件准备:该软件是某实验室自行开发,较类似软件优点是除按位号寻找位置外,还可采用封装形式、 规格、方向(吸嘴转动角度)为选项。可选择在板边(如图一边框处)与定位点(图二焊盘间)同时显示, 并可仅显示板边, 或仅显示定位点等三种显示方式。以Gerber为平台精准指示相关位置。并可使众多同类别选项同时显示,较一些品牌软件也极具特色。当显示屏幕足够大时,用于虚拟首板确认,其优势将更加明显。当贴片程序(来自(BOM))被导入此软件后,配合与BOM核对。在用于虚拟的机贴物料的首板确认时。可挤兑出自BOM转换(BOM)时可能的错误。而导入项为(BOM)与CAD时,则可根据工序分类按规格生成手贴、手吹、插件等简易作业指导书。
图一:选择参数值部分电容10N 0402,找到76个匹配项,板边和定位点同时显示。
图二:对图一文件进行局部放大。
4、虚拟首板确认:把贴片程序中的位号与坐标导入到找位置软件,注意此时的原点与Gerber并不一致,应做offset修正。再按(BOM)的序列号从小到大,逐一选择机贴物料规格为显示项。则所有相应的位号可显示在GERBER示图四周(板边),如图一。以这些依次排列的位号与BOM中相应的位号对照并用铅笔标注,可以确认程序中位号数量与位置的正确性。此时标识点(定位点)剪头方向对应于物料的极性如图二,可以做为极性正误的判据。当选用标识点显示在贴片焊盘位置正中时,如图四。则可判定坐标位置的正确性。因许多物料的CAD数据并不以器件的几何中心为基准,在此可以根据标识点与焊盘的非对称性提前识别,免得上机后才发现座标有误。另一识别是按封装如0805为选项。如图三显示,看所有0805焊盘大小是否一致,以便事先发现物料与PCB 上相应焊盘的不一致性。
图三:选择封装形状0805封装找到57个匹配位置,只显示定位点边提示。
图四:对图三文件进行局部放大。
5、 丝印机、贴片机支撑图准备:印刷机B面的支撑图,当用平面支撑时可省略。其余的要用透明薄膜以1:1的方式把GERBER图B面与T面的位号及焊盘层打出。支撑的选点要把二者重叠后确定。用于B面的支撑点要尽量避开T面的BGA、QFN等各种微小焊盘,用于T面的支撑则要尽可能撑实BGA、QFN、连接器等细间距物料下方。同时要防止碰伤B面物料。固定间距的支撑销较磁性支撑销有更多的限制(若能采用可变间距支撑销则可有较好的结果)。应配合定间距网格选点,同时注意STOPER的影响。选点完成后用红色油性笔在透明膜上做记号,并标出进板方向。编号说明产品名称,适用机器及适用面。从质量成本考虑,支撑不论对印刷机或贴片机,都是极其重要且最易被人忽略的品控关键点。
二、 物料管理
1、物料的接收: 要尽量简化,小批量时来料多为小段齐头料,托盘料一般也都不正规。某司早期接料经由市场,采购,库房以及IQC,才到生产班组。反复的清点与检查,使物料状态更加恶化。变形,可焊性变差,在貌似正规的制度下造成了许多可避免的麻烦。事实证明,物料直接由专职操作员接收是较好的选择。该人负责发料清单与(BOM)的对应及核实。重点是物料的规格及封装,对chip件的数量确认不应强求。称重是应首选的确认数量的手段。
2、物料的标注:在物料的最终包装上贴上纸胶带,写上(BOM)中该物料对应的序列号。再根据机贴程序,手贴工艺,手吹工艺、手焊工艺(含压接,铆接,组装)分别标注缩写。如:机,手,吹,焊。并要标出用于哪一面。在T面标T,在B面标B,T与B面均使用时标T/B。标完后按T面, B面及T/B面及工序分开放置。以利于工作时有序找料。且在(BOM)序列号处做有料标注,以便核对(BOM)上所有物料是否己齐全。注意在物料的标记时,要确认实际封装如0805与(BOM)所写封装的一致性。当发现预定机贴物料有变形及不适上机的状态及时转手贴。要鼓励此时对前期文件处理的修正。
3、物料关注重点: 首先要判断PCB是否有电测试痕迹,用30x放大镜看焊盘上的针痕。若无,(BOM)备注上应标出。并测裸板各电源端对地有无短路(以后各工序都增加对各路电源的短路判定)。PCB一般应无条件烘烤且整平,注意工艺边是否足够,有问题标在(BOM)上。小批量时不影响功能的缺陷,当有可能影响交期时应考虑放行。同时告知客户。确认所有极性元件是否在PCB上有相应的白油标识,若无则应在PCB上做永久性极性标识。有金手指,金键盘时要事先于办公区做贴保护,有试锡板时确认一下可焊性。对PCB上BGA类的非可视焊点焊盘,有疑似可焊性不良时,可用烙铁手工上锡后整平待用。PCB外形的目视检查重点是夹持边的毛碴。
其次是接插件、压接件、铆接件都要试插或者比对一下,如果物料不适,优先改造PCB以适应物料(在裸板状态,修改起来要简单得多)。
QFN电极如立面无涂复保护,且疑似可焊性不良时,应手工在电极立面搪锡。
4、网版与工装的导入:项目工程师要参与对物料的查看,以异型贴片件和未见过的封装为重点。一定要认识到,当你不能干预PCB的DFM时,网板开口的补救措施是最有效的品质保证手段。一般是把异形物料电极向上放在焊盘旁,目视其间的差异。按网板开口原则处理(参照贾忠中[SMT核心工艺解析与案例分析] 一书)。当有PITCH<0.5mm的物料时,OFFSET式网板开口在焊盘间有走线,但无阻焊层时应优先考虑。
当你在短时间内,对确认印刷参数无把握时。网板厚度宜薄,以得到稳定一致的焊膏量。开口宜稍大以对应小批试制时物料可焊性多数无保证这一事实。在网版面积许可的条件下,可在一块网版上有两个不同的开口设计方案,以增加现场的对应能力。最好能采用局部DEK膜工艺。对纳米涂料的预分装及热合再封装是低成本的要点。
工装因使用次数少应采用低价材料,但关键部位要采用高精度的加工方式以保证使用。其余辅助部分可用后粘合方式,以降低成本。
有面积较大的压平结构时要考虑实际效果,尽量不采用面对面的压平方式。用线对面的压平方式低成本,灵活性好,效果也好。
测温板应使用产品用PCB,关键器件只能采用替代品,在厚度及体积方面的相似性越大越好。能有类似的报废板由客户提供是最佳选择。热电偶选点参照“测温板制作方法”(参照2014论文集 三重 尹华春)。
炉温曲线的确定应事先完成。应偏向直通率考虑,峰值就高不就低。充分考虑物料特性,如焊球合金成分,BGA的尺寸,厚度,类型。铝电解,接插件要事先过炉看其温度耐受性能。对薄板,多层板的二次过炉优先考虑简易载具,保证PCBA的平整度。室温至峰值时间与焊膏特性差异要小,在含微小焊盘的生产时尤为重要。提倡上下温区差异化的设置方式。
三、现场管理
1.物料准备(上线两小时前应已完成)
1-1、所有托盘料的烘干,首选真空烤箱 125°C/2~4H。
1-2、无铅工艺PCB或多层PCB参照上条。
1-3、金手指,金键盘贴保护(于无焊料粉的办公室或会议室)。
1-4、PCB编号并标识,无测试痕迹时所有电源回路短路判别并记录。
1-5、QFN电极立面无涂覆,且可焊性疑似不良的器件手工在立面搪锡。
1-6、锡膏回温4H,再甩90s。
1-7、PCB贴无残留膜,最少四块。
1-8、网板清洗,有脱模不良可能时局部涂DEK膜(纳米涂料要分装,一分四后用热压机封口。每1/4包装可对应4~5块网板的局部开口)。
1-9、准备精密天平(精度10mg),所用焊膏的原厂供助焊膏。水金PCB或疑似物料可焊性不好时,应在陶瓷板上做试验。确认不良后加总重0.5~1%的助焊膏。
1-10、HASL板MARK的平整度确认,应小于15um。否则用烙铁与吸锡绳抹平后用黑橡皮打磨。
1-11、所有支撑,工装的清扫。
1-12、手贴件与手吹件分别连料带用双面胶粘在防静电板上,每种料都标明(BOM)的序列号及单板用量,并标出单板用量所对应长度。
1-13、无标识的CHIP料要用LCR表判别其阻抗正确性。
2.印刷工序
2-1、所有未贴膜的PCB用胶滚去异物。
2-2、利用支撑图快速建立支撑,B面时优先用平面型支撑。
2-3、真空清扫口两边用胶带封住,仅留和PCB等宽开口(国产机尤是)。
2-4、试印第一块贴膜PCB,检查位置偏差并纠正。最少陆续印四块贴膜PCB后,才可正式印刷。
2-5、正式印第一块生产用PCB,此时最小开口的脱模状态可能会劣于贴膜PCB。若在可接受的下限时,则每次清扫都要选择真空模式。慎用压缩空气吹或用湿巾以手工模式过度清扫,那样会使开口壁上助焊剂流失。而使转移率进一步下降。
2-6、在得到可接受的印刷结果后尽快全数印完。有缺陷时,按PCB编号记录缺陷位置,本着宁修勿冼的原则,尽量不要清洗印刷失败的PCB。能有富余的PCB备份为最好。否则用银针补焊膏,但应取自试印膜上相应焊盘的焊膏。焊接后在该位置用目视或者X-ray重点检查。
2-7、印刷机收尾由机贴操作者完成,其在下工序工作时间以及内容要少于手贴操作者。
3.贴片工序
3-1、手贴在第一块PCB印刷完毕后尽快开始,要与机贴并行工作。手贴建议同时贴几块板的同一种料,而不是一块贴完再贴一块。这样对出错率和效率都有好处。
3-2、手贴完一块板后,要在料带旁标识以证明所用数量是正确的。每一种物料在单板贴完后应在粘料板上写出相应PCB编号。在出现问题时可用较少的时间判定症结所在。
3-3、手贴工具以吸笔为好。当用防静电镊子时,歪件后尽可能拨正即可,不要重夹起来。镊子尖要勤清扫,贴放后应有点压动作。除QFN外,较大封装IC尤应施加较大的压力。
3-4、QFP,SOP引脚疑似可焊性不良时,引脚没入膏的深度较大时焊后结果会较好,但chip类则不应有焊膏被挤压的痕迹。
3-5、当有印刷错位时,贴片应以焊膏为基准以得到尽可能满意的结果。
3-6、当某局部间隙极小(如0.13mm以下)时或对位置要求很高(v-cut槽旁)。灵活运用offset模式贴偏一些,让chip在回流时自动找正位置可降低不良率。在LGA对空洞要求严格时也可斜方向贴偏0.05mm。
3-7、当贴片收尾有少料情况时,一律不找料。跳过后按PCB编号记录即可,以后以修理手段补上。
3-8、推定易产生吸着不良的物料,如0402及以下chip或者较重的物料。要放慢吸取及运行速度。在首板时,每贴100件chip要停机检查一下有无飞片现象。500件后无异常则可不再停机检验。可能时优先贴非chip物料。
3-9、生产最好安排在周保养后,至少要清洗吸嘴并更换过滤棉。
3-10、大件,高重心,易浮起件应是炉前检查重点。安排在炉前过桥处手贴。机贴已完成的PCB,手贴时优先贴BGA,QFN等焊点不能直视的物料。
3-11、首板机贴后没有停机确认的过程,立刻打第二块板。然后仅确认首板机贴件的方向是否正确。不能确认的做记录。
3-12、变形的器件要修正后再贴,并做记录以利最终的针对性检验。
4.回流工序
4-1、炉前检验所有有极性器件,压实易浮起器件。
4-2、B面原则上一律走网,给T面印刷打好基础。
4-3、进炉时PCB间距尽可能大于板长的3倍以上。
4-4、走网时避开通长的网带支撑条,至少使其不位于关键元件下方。首板过炉前可放2块热容量相似的PCB于其前方3倍板长处。
4-5、首板的焊接状态确认后方可接着过板,重点确认BGA的塌陷程度和大型物料的焊点状态(有无冷焊),微小焊点(0402或者以下)有无葡萄珠现象。微小物料有无因风速导致的缺陷。连续过板完成后,马上两人同时收线,尽快让他人转线进行下一产品的生产。
四 质量成本管理 (以下与占线时间无关)
1-1、炉后尽量使用叠式存储器放置刚出炉的PCBA,在托盘立放可能使PCBA产生翘曲,且板边的物料有与托盘凹槽碰撞的可能。
1-2、单边尺寸大于150mm的PCBA不可单手持着,一定平放在有防静电海绵的钢性托盘上,后工序均应按此处理。
1-3、BGA目检后用无残留胶带封住四边间隙,按手吹指导书完成剩下的贴片料焊接。原则上仅能使用热风枪。
1-4、目视检查重点是曾出现印刷缺陷的焊点和疑似可焊性不良的物料的焊点。所有不良处用红箭头标识指出。
1-5、不良点的修理完成后在红箭头上用笔标识。在QC确认合格后并填写直指原因的修理记录后, 撕去红箭头。
1-6、铆接时注意方向,手工压时可分两三次加力完成压铆,以减少可能的失手,机压时尽可能放慢速度。
1-7、压接每种规格物料的第一个时要尽可能慢,PCB与下模的对位与方向性要格外小心。从成本出发,小批量时手工为宜,最好不要一次压到位。每次加压后要检查有无跪腿现象。上模一定要用高精度的,事先要用实物验收,看精度是否合适。当有两个压接件紧密排列时要注意上压头的外型是否会干涉先前压好的件。压接件孔径要事先确认。HASL孔可用合适的钻头过一下,以消除喷锡使孔径变小的缺陷。
1-8、直插件尽可能成型为短插以消除以后的剪腿工序。
1-9、当透过率不好时应该避免两面焊,用热板以125°的温度预热并在引脚上用助焊笔凃助焊剂是比较好的选择。
1-10、多引脚物料先对角定点,确认无浮起后方可进行下一步的焊接。
1-11、晶体的金属外壳原则上不要焊接。
1-12、无铅的手工焊接要时刻想着铜蚀的风险,用SAC305锡丝的风险远大于锡铜焊锡丝。
1-13、有分板需求时一定要小心应力的作用,没有可靠对策时,切忌蛮干。
1-14、包装要用ESD材料,箱内空间要填实,充分考虑运输中可能出现的野蛮状况。
1-15、一般不采用在线AOI。
1-16、BGA, CSP, QFN尽量全数过x-ray,重点是查虚焊。
1-17、目检采用比对方式,如用1号板与其余板对照检查。标记出差异待核实。首先看空焊盘的一致性。重点是非机贴物料的方向以及标识的一致性。焊点目视重点是模块以及QFN。其次是细间距的QFP,SOP以及连接器(p<0.5mm)以及有整形记录的物料的焊点。
1-18、把DFM相关内容反馈给客户以便今后从源头解决问题。写试制报告, 所有不良项要认真解析, 并总结在时序上的浪费。
致谢:感谢曾经的团队成员陈克鑫、冯桂玲在多次的实践中提出的宝贵建议及在现场不懈的努力。
如需看完整的技术文章:请订阅印刷版《SMT工艺与设备》杂志/电话:0755-25856945
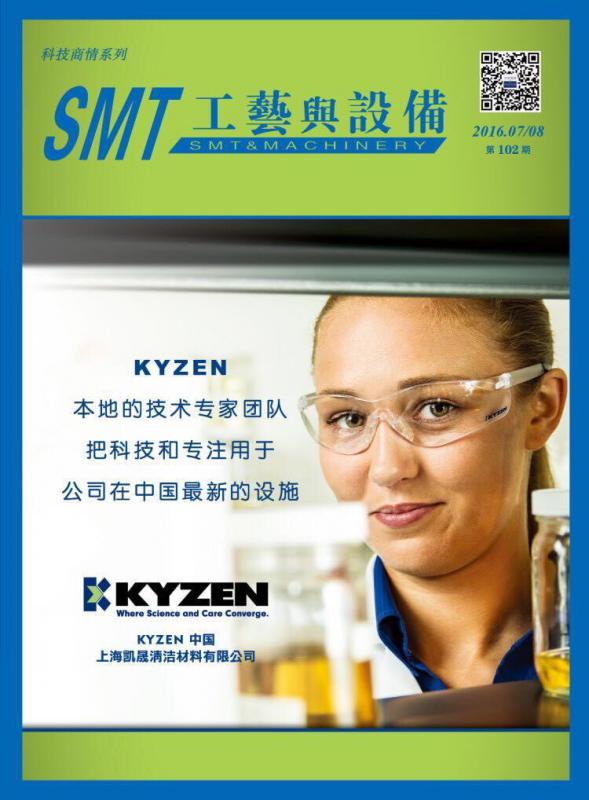
版权所有 ©深圳市亚中咨询有限公司
电话:0755-25856945 邮箱:pzl88smt@126.com 网址:www.smt668.com
地址:深圳市罗湖区怡正发大厦 SMT专业网版权所有(c) 2010 粤ICP备17073069号
本站部分图文来源网络,如有侵权问题请通知我们处理!
网站建设维护